Glasshouse Interconnect Cable No.3
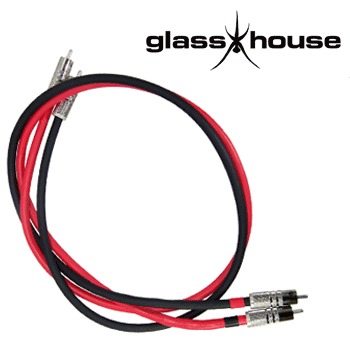
The design philosophy behind the Glasshouse screened interconnect cables is to produce a set of premium quality interconnects using components of the highest quality resulting in a cable with superb sonic properties and excellent extraneous noise rejection. These cables are a development of the Glasshouse Interconnect Cables No.2, using three strands of Mundorf's 99% silver / 1% gold 0.5mm single core wire, sheathed in PTFE as the main signal carrier. However, these cables are also fully screened and terminated with Cardas SLVR SS silver-plated phono plugs.
In order to make up the interconnects, three strands of the Mundorf cable needs to be weaved together to form the signal conductors. There are various schools of thought on what method should be used: twisting together to form a rope, various methods of weaving or just leaving the wires loose to be threaded into screening and sleeving. Leaving the wires loose will result in a random layout within the wire which may produce undesirable effects. Twisting the wires together will tend to increase the inductance of the wire and will shorten the resultant cable by a small percentage, from experience. Weaving the three strands together in the form of a plait results in no significant change to the length and minimises the cable inductance. It is also relatively easy to do by hand. This was the method chosen for these interconnects.
Listening Test:
Before attempting any comparative listening tests, it is very important to burn-in the cables for between 70 and 100 hours. However, the first 10 hours makes a huge difference to the sound, in my experience, and then continues to improve in a more gradual fashion. The signal flow in a cable can be compromised by a number of factors such as resistance, skin effect and capacitance, inductance, RFI, and dielectric material. All of these factors can affect the transfer of complex musical signals. Burning in a conductor affects the crystalline structure and allows many of these variables to settle down which has a positive effect on sound quality. I achieved this by feeding the cables from a radio source with the power amplifiers switched off, but HiFiCollective can provide a cable burning service if desired.
For my tests, I was using a set of 'standard' high purity copper coaxial cables that had been in use for some time. If you are tempted, like I was, to test the cables immediately after construction, you may well be disappointed. In comparison to my fully run-in cables, the new ones sounded a bit harsh in the top end, although the bass was more extended from the onset. One of the problems I had experienced with my copper coaxial cables and others I have used was interference from my BlackBerry/mobile phone if it was in the same room as my Hi-Fi. Whenever it connected to the network to update emails, etc., I could hear a loud buzzing through my system. With the Glasshouse cables, this was virtually eliminated - a very good start!
However, after the first 10 hours of burn-in, it was a very different story! The top end became clearer and less harsh. The midrange re-appeared from the shadows and the already extended bass became tighter and better controlled. The overall effect when compared with the copper co-ax was that musical instruments sounded more real. This was best illustrated with my 1979 vinyl recording of Beethoven's Piano Concerto No. 5, "The Emperor", on Decca Digital Master SXDL 7503. The piano, one of the hardest instruments to record and reproduce, became more alive in my sitting room.
On the lighter side, I am fortunate to have access to a large amount of music used by the BBC that accompanied the test card and used as intermission music between schools programmes and 'rain stopped play' intervals in the 60s, 70s and 80s. Most of this music was recorded using full orchestras or small groups of individual musicians in superb quality. Alas, such recordings would be prohibitively expensive to make today. When transcribed onto CD from the original master tapes by highly skilled people who understand the music of the time and using the latest technology, the results are recordings of unsurpassed quality without any of the modern shortcuts using synthesised sound. These recordings make superb test recordings and I could write pages detailing the differences, both subtle and dramatic, on every instrument that the new cables reveal over my old copper cables. However, I can summarise them by saying that the new cables add a new dimension of realism, detail, clarity and presence to every individual instrument, whether in a small ensemble or a large orchestra. In conclusion, do not underestimate the difference a set of high-quality interconnect cables can have on the sound of your system. It is also vitally important to burn-in the cables before attempting comparative testing. These cables are a real bargain as, being a kit, you are saving money as you are only purchasing the composite components. The mark up of the components is a fraction of the mark up of a manufactured and fully burnt-in cable, so it is easy to see why some interconnects can cost thousands of pounds. You will not be disappointed in the Glasshouse screened interconnect cables - treat yourself!
Instructions: Please refer to pictures 1-7
- Cut the supplied Mundorf wire into six identical lengths (three for each cable). Clamp the ends of three of the wires firmly, but not so tight as to damage them. I found that inserting them under the leg of a table to be a suitable method.
- Now roll up the three wires loosely and put each roll in separate recloseable plastic bags, such as the ones used to supply the components in. This makes the wire easier to handle. Now plait the three wires together neatly by moving the left wire over the top of the middle wire, so it is now in the middle. Then repeat for the right wire moving it over the top of the middle wire so it now occupies the middle position. Then repeat the process with the 'new' left wire, and so on. After doing this five or six times, neaten up the plait by holding the cable taught and squeezing the plait up towards the clamped end.
- Your finished weave should look like PIC 3. Repeat for the other cable using the remaining three wires.
- The next stage is to pull the wires through the braid screen. The braid is supplied with a hollow plastic inner sleeve which holds the braid in place. To make the two cables, cut the braid in half and remove the braid from the inner sleeve by compressing it slightly along its length. This will increase the diameter of the braid and it will slip off easily.
- Now solder the three wires together and solder these to the single strand of spare wire provided that can be threaded through the sleeve first. Incidentally, to strip the PTFE from the Mundorf silver wire, slightly squeeze the end of the wire with snipe nose pliers, lay the end on a cutting board and with a trimming knife carefully cut along the length. You should be able to peel back the PTFE and cut off the excess. Slowly pull the wires through the sleeve and you should end up with the wires as shown in PIC 4. Now slip the braid back over the sleeve and pull it back to the whole length so it fits snugly on the sleeve again (PIC 5).
- The next job is to slip the heat shrinkable sleeving over the braid. This simply slips over the cable and is shrunk onto the braid by moving the cable over a gas flame. Keep the cable moving from side to side and rolling it over to avoid localised overheating to shrink the sleeving smoothly over the braid (PIC 6).
- At this point, it should be mentioned that the screen should be connected to the earth at one end of the cable only, corresponding to the star earth point of your Hi-Fi system. This prevents any chance of a hum loop occurring and connection at both ends is not required as the signal earth is connected via two of the Mundorf wires. If you are using the cables to connect between your preamp and power amplifier, the braid earth is at the power amplifier end. If connecting a source, such as a CD player, to your preamp, this will be at the preamp end. Hence you will need to insulate the braid at one end and have it extending from the sleeve at the other ready for connection (PIC 6).
- The Yarbo plug shown in PIC 7 allows for soldered connections to both the centre spigot and the earth. The latter connection is made on the little ring below the thread that stops the heat from the soldering iron from being conducted away by the metal body. Before connecting the phono plugs, slip the two outside rings from each phono plug onto the wire, being careful that the four rings face in the appropriate direction for their respective phono plug. To indicate the screen connection end, use the aroow labels, pointing to the screen connected end. Incidentally, this effectively makes the cables directional and once burnt-in, the identification will prevent the cables from being connected the wrong way around.
- Using a multimeter, identify both ends of a Mundorf wire to use as the signal wire and mark with a felt tip and solder up the plug. PIC 7 shows the braid end making contact with the phono plug shell prior to fitting the two rings in place to complete the cable termination. Repeat for the other cable and your interconnects are ready for use.
Contents: (for a pair of 1m cables)
- 2m x Mundorf wire SGW305, 3x0.5mm 99%silver/1%gold twist
- 4 x Cardas SLVR SS male RCA plug, silver plated
- 1m x Mundorf 3.8% silver/gold solder
- 2m x Screening Braid: BTUBE 4mm
- 20mm x HTSB12.7, Black heatshrink 2:1, 12.7mm diameter (for end markings)
- 20mm x HTSR12.7, Red heatshrink 2:1, 12.7mm diameter (for end markings)
Outer sleeving:
- 1m x HTSR9.5, Red heatshrink 2:1, 9.5mm diameter (Shown in image)
- 1m x HTSB9.5, Black heatshrink 2:1, 9.5mm diameter (Shown in image)
Option:
- 2m x Cotton Tubing: COT-10/11
PRICE (from)
£210.27 +vat +p&p