V-Cap CuTF Copper Foil Teflon Capacitors
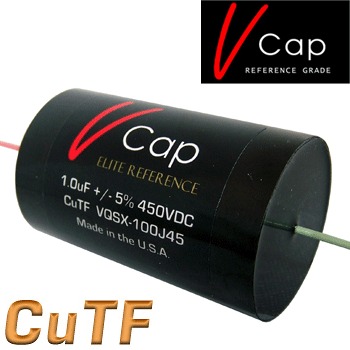
The CuTF series provides the musicality of pure copper foil with the expertise, materials, and processses of the most innovative companies from around the World. If your gear is capable of delivering an out-of-body experience, install the new CuTF series and connect to the soul of the music... Recommended for signal coupling in valve electronics, speaker crossovers, and guitar electronics.
After nearly 5 years of intense R&D, I am pleased to announce the new V-Cap CuTF series- an audio signal capacitor that will take you to the Soul of the Music...™ Chris VenHaus
Which way round do they go?
The green lead indicates the outermost foil, and should be connected to the lowest impedance path to ground. Another way to identify outer foil is the writing on the label flows towards the outer foil.
When used in amplifiers, outer foil should be connected towards the anode of first stage If using as a bypass cap to ground, connect green lead to ground. If using as a bypass cap from a signal to B+, connect green lead to B+. If using in a feedback position, connect green lead towards the output.
Specifications:
- Lead material: 18 AWG solid core high purity OCC (Ohno Continuous Cast) copper with VH Audio’s AirLok insulation- a proprietary form of foamed/cellular Fluoropolymer with a Dieletric Coefficient of less than 1.45.
- Pure Fluoropolymer film dielectric. Cheaper forms of PTFE and FEP can be sourced (some cast, some skieved), and we tried them all. "You get what you pay for" was especially true when it comes to sourcing generic fluoropolymer alternatives to genuine DuPont Fluoropolymer , based on our listening tests.
- Oxygen Free High Conductivity copper foil ( IACS of 101%). Our copper foil is rolled to extremely tight tolerances using state-of-the-art machinery and computerized electronics that constantly monitors the foil in real-time, and makes corrections while the material is being rolled. Even the rollers are machined in-house to ensure a smooth and consistent surface finish. This quality and precision is unmatched by any other company in the world.
- The copper foil is dead-soft annealed in an inert atmosphere, and treated with an anti-oxidant bath before being slit with blades that might rival the edge of a Hanzo sword.
- The copper foil is vacuum packed before undergoing our proprietary Cryogenic treatment process (below -300 degrees F) . We’re not talking about throwing some copper out in the Frozen Tundra overnight, but rather a $50,000+ state-of-the-art machine that uses custom profiles, and molecular kinetics to avoid any thermal shock to the material.
- Fluoropolymer film slitting is performed in-house, which means better control over environmental cleanliness, as well as frequent renewal of the slitting blades. You won't find a messy guy with a butterknife anywhere near our film.
- The winding process is performed in a clean, controlled environment on custom, internally-built manual winding machines. A select group of dedicated Master Winders (averaging over 14 years of experience) perform the winding operation with meticulous attention to every detail. Their pride of workmanship is simply unmatched, anywhere.
- A new lead attachment technique was developed to maximize contact surface area with the winding and keep ESR astonishingly low, and extremely consistent from part to part.
- The core of the capacitor has been engineered to optimize the structural integrity of the winding, as well as to address internal resonances that may smear the audio signal.
- Dimensional ratios were carefully chosen for each value, based on listening tests specific to this construction type.
- Capacitor end fill was carefully evaluated, based on sonics, as well as its long term inertness and mechanical stability. The end fill process itself is quite lengthy and requires numerous steps that were perfected over years of experimentation.
- At several checkpoints during the construction process, every capacitor is tested to meet several critical electrical measurements and mechanical inspection criteria. No simple "batch testing" is performed- it's not good enough.
- An extensive, rigorous testing and burn-in protocol was developed to ensure the highest performance and reliability in the extreme environment found inside equipment that uses vacuum tubes. The sheer number and extensiveness of these electrical tests is well beyond industry standards.
If you are looking for a specific value, we have added a CAPACITOR FILTER to speed your search up.